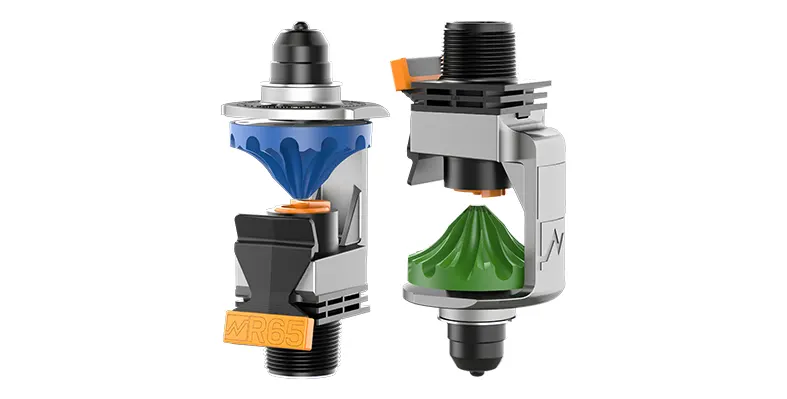
These new additions are designed to improve upon the performance of the well-known R55. (Image credit: Nelson Irrigation)
Nelson Irrigation has introduced two new models to its end-of-pivot sprinkler line: the R65 VT and the inverted R65i VT
These new additions are designed to improve upon the performance of the well-known R55, with a particular focus on increased reach and enhanced water distribution uniformity. Both sprinklers operate efficiently within a low-pressure range of 15 to 60 psi (1 to 4 bar), delivering flows from 4.3 to 23.6 m³/hr (20 to 106 gpm). Their throw radius spans from 10.6 to 16.4 metres (35 to 54 ft), allowing broad coverage across diverse field types.
The design upgrades include a slimmer body and a more advanced nozzle system that helps achieve better distribution even under lower pressure conditions. These improvements make the R65 series highly adaptable for a variety of pivot irrigation setups. Farmers can use these sprinklers to cover the entire pivot circle, target corner areas, or work in conjunction with a high-volume Big Gun® sprinkler, depending on the needs of their fields.
The inverted model, the R65i VT, has been engineered for easier installation and improved flushing performance, thanks to a newly designed green plate. This feature is particularly valuable for maintaining reliable operation at the far ends of irrigation systems. Both versions use focused water streams that enable longer throw distances and feature a 270-degree spray pattern. This pattern is designed to irrigate behind the sprinkler, overlapping with the pivot’s regular sprinkler layout to maintain consistent soil moisture even at the field’s outer edges. The updated #90 nozzle works seamlessly with the green plate, simplifying maintenance and improving compatibility across components.
One of the standout features of these sprinklers is their integration of Nelson’s Rotator® technology. In use for over three decades, this technology is known for its ability to produce strong, wind-resistant streams that deliver water more evenly than traditional droplet-based methods. Rotator sprinklers also reduce application intensity, which allows for better soil absorption and less surface runoff.
In summary, the R65 VT and R65i VT offer a smart, durable solution for modern pivot irrigation systems. They bring together energy efficiency, even water application, and dependable performance—all tailored to help farmers achieve more effective irrigation with less input.