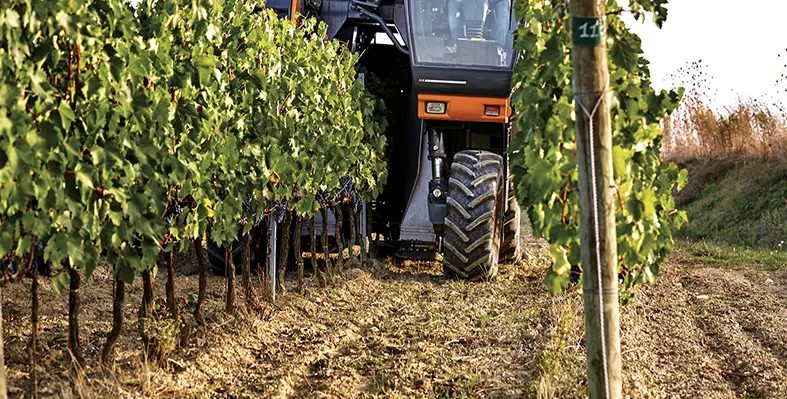
Utility tractors are compact, fuel-efficient, and easy to operate. (Image Credit: Balkrishna Industries Ltd.)
In today’s agricultural landscape, utility tractors—often called ‘wildcard’ tractors—remain one of the most sought-after and strategic choices for small to medium-sized farms
With power outputs ranging from 70 to 130 horsepower, these machines are designed to handle a wide array of tasks, from light fieldwork and transport duties to front loader operations in tight spaces such as barns, vineyards, and orchards.
Versatility is a cornerstone of utility tractors, and tyre choice must mirror this adaptability. That’s where Balkrishna Industries Ltd. (BKT) steps in. BKT offers customised tyre solutions, blending advanced technologies and modern compounds to deliver tyres that are reliable, durable, and fit for varied terrain and tasks.
Utility tractors are compact, fuel-efficient, and easy to operate—qualities that make them indispensable for day-to-day farming activities. Their ergonomic design guarantees comfort during extended operating hours, while their powerful traction and manoeuvrability allow productivity even on loose or uneven soil. Whether it’s ploughing, weeding, transporting hay, or navigating narrow barns, utility tractors offer unmatched flexibility.
BKT provides tyre models specifically designed for utility tractor use in order to support these demands. These include:
AGRIMAX RT 765 – Excellent for open-field use, offering even weight distribution, reduced soil compaction, and strong self-cleaning properties.
AGRIMAX RT 855 – A versatile option suitable for multiple terrains, delivering high traction and tear resistance. Ideal for tractors frequently moving between the field and the road.
AGRIMAX RT 657 – Reliable for both tillage and road transport, with select sizes suitable for grape harvesting. Noted for its comfort and fuel-saving design.
BKT continues to support evolving agricultural practices by developing tyre patterns that meet the real-world needs of utility tractor operators. With durability, performance, and operator comfort in mind, BKT’s solutions help farmers maximise productivity and manage agricultural resources more effectively.