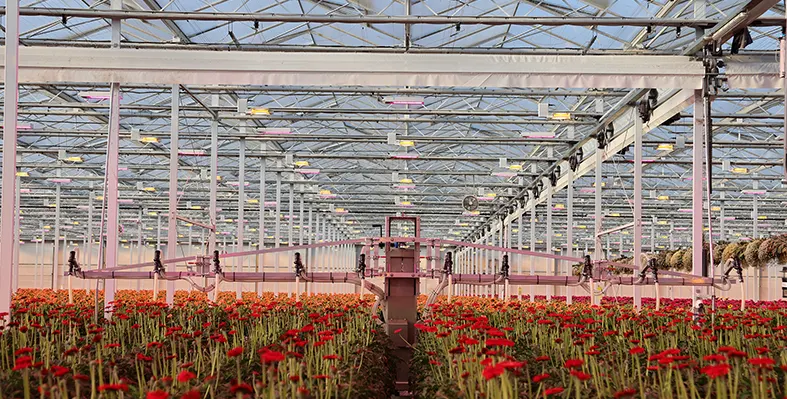
Entomatic is highly versatile and can be used in horizontal and vertical row crops. (Image source: Biobest)
The Entomatic automated dispenser stands as a game changer for spider mite control, ensuring precise and uniform Phytoseiulus distribution across crops
Phytoseiulus persimilis, a specialised predatory mite, feeds exclusively on spider mites and is an essential and well-established component of biocontrol programmes. Entomatic is highly versatile and can be used in horizontal and vertical row crops. It has been widely adopted in high-tech protected vegetable crops, such as tomatoes, sweet peppers and cucumbers, as well as cut flowers and open-field strawberry production.
Beyond Phytoseiulus-System, Entomatic efficiently distributes other predatory mites, most beneficial insects, and Artemac supplementary predator feed in tomatoes. Its user-friendly, modular design allows for easy configuration across different glasshouse setups, whether mounted on existing carts, tractors, robotic sprayers, or custom driving platforms.
Sam Gui, market development manager for High Tech IPM at Biobest explained how Entomatic maximises effectiveness by smoothly and precisely releasing Phytoseiulus-System, at a controlled rate, over the head of the plants. “Aside from the increased precision, due to automatisation, Entomatic can significantly cut labour costs. Depending on the Entomatic model, we’ve seen labour costs for beneficial mite introduction cut by up to 90%.”