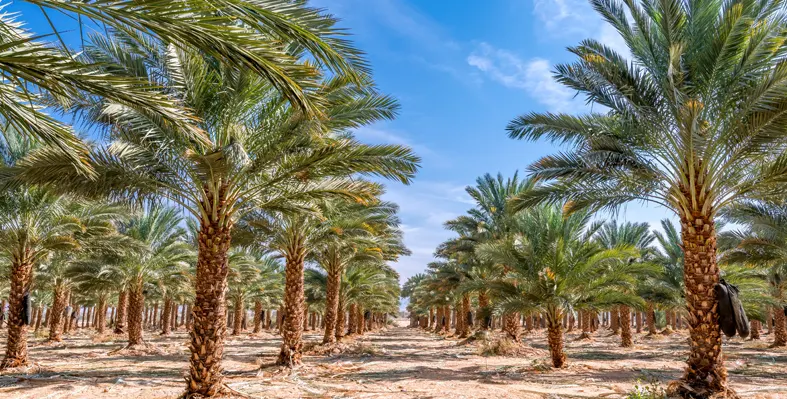
Desert Control deploys soil-saving tech across 160 acres of Oasis Date's organic Medjool date palms in California. (Image source: Adobe Stock)
Desert Control AS, a pioneer in soil and water conservation technology, has secured an agreement through its U.S. subsidiary, Desert Control Americas Inc., with Oasis Date, North America’s largest date grower and processor
The partnership will deploy Desert Control’s Liquid Natural Clay (LNC) solution across 160 acres of organic Medjool date palms at Oasis Date’s Corn Springs Ranch in California.
The NOK 1.5 million deployment follows a successful pilot project initiated in July 2024, which covered 13 acres of date palms. The pilot showcased notable improvements in water retention, soil health, and overall performance. The expanded 160-acre rollout, scheduled for completion in Q1 2025, marks a significant step in scaling Desert Control’s innovative soil and water conservation technology across Oasis Date’s operations.
“Oasis Date is setting the standard for sustainable and regenerative agriculture, and we are proud to collaborate on this initiative,” stated Ole Kristian Sivertsen, CEO of Desert Control. “By implementing Liquid Natural Clay, we can help Oasis Date conserve water, improve soil health, and enhance yields, reinforcing their position as a leader in environmentally conscious farming.”
Managing over 5,000 acres of date farms and producing over 1 billion dates annually, Oasis Date is the majority supplier for Natural Delights, North America’s top Medjool date brand. As the world’s first and only Regenerative Organic Certified date farm, Oasis Date exemplifies its commitment to environmental sustainability and farmworker welfare.
“Oasis Date is a strong leader in their industry, and their dedication to sustainability and regenerative farming practices aligns perfectly with our vision,” said Marty Weems, managing director of Desert Control Americas. “We are honored to work with Oasis Date utilising our soil and water conservation technology to reduce operational costs and safeguard the long-term prosperity of their ranch and farming operations.”
Desert Control’s LNC technology transforms sandy, fast-draining soils into fertile, water-retentive ground, reducing irrigation needs and promoting healthy plant growth. This collaboration also opens opportunities for broader adoption of LNC technology across Oasis Date’s extensive operations in California and Arizona.